Primary Size Of Roll Mining Mill How Much
.jpg)
Hammermill and roll crusher maintenance and
2023年6月21日 Hammermills are sized using a ratio of screen area to connected horsepower For most applications, 14 in²:1 hp is the preferred ratio Some applications, such as products with a lower bulk density, may require 2023年1月1日 Scaling up HPGRtower mill comminution circuit should consider size reduction ratio This paper presents the commercial implementation of a novel comminution circuit with Evaluating the performance of an industrialscale high 2023年7月4日 Roller mill is a type of grinding equipment for crushing materials by pressure between two or more rolling surfaces or between rolling grinding bodies (balls, rollers) and a Roller Mill Springer2022年4月1日 For grinding it used primary rod mills, secondary and tertiary ball mills to reach the secondary copper flotation size P 80 of 44 μm, and two regrind mills per circuit for copper Keys to best practice comminution ScienceDirect
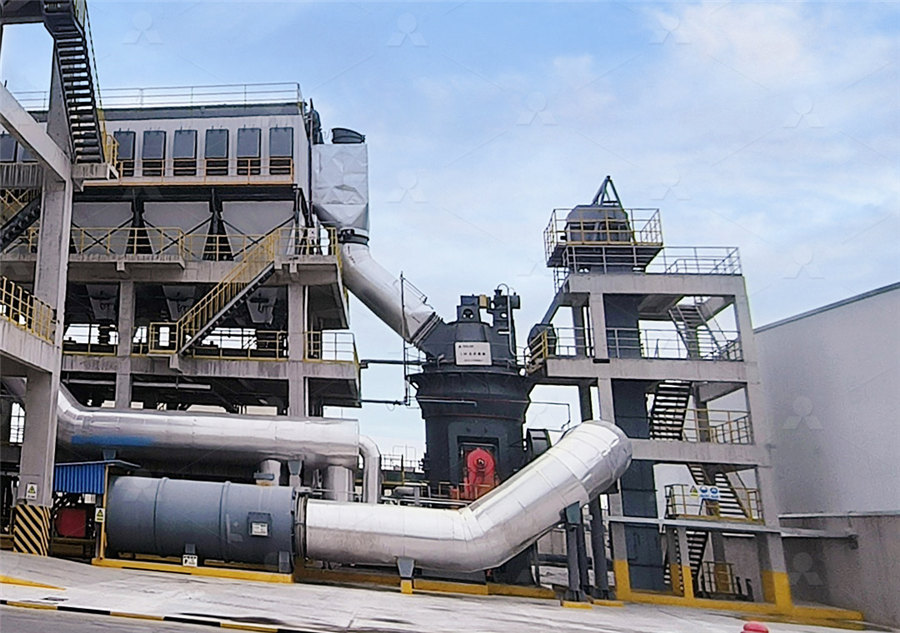
Potential of HighPressure Grinding Roll (HPGR) for Size
2022年3月16日 HPGR has been found to be efficient size reduction equipment compared to conventional size reduction equipments due to its potential processing benefits in terms of INTRODUCTION Primary grinding mills as defined in this paper, are autogenous or semiautogenous rotating, tumbling mills having a coarse feed with a top size usually varying from Primary Grinding Mills: Selection, Sizing And Current Practices2023年8月5日 In summary, in fact, most of the factors affecting the output particle size of the highpressure roller mill are in the operation mode When the appropriate roller surface Factors affecting the particle size of the highpressure roller mill2015年9月20日 large ball mills to complete a full size reduction from runofmine (RoM) feed to flotation feed in three stages There are two ore feed conveyors, from primary crusher to (PDF) FULL PRECRUSH TO SAG MILLS ResearchGate
.jpg)
Vertical roller mills: The new leader in grinding technology
2019年10月11日 The VRM, depending on the roller size, has a high reduction ratio; feed from 80 mm to 140 mm to a product of P80 at 75 µm in one pass, the mill is a closed circuit on its own 2017年6月2日 During the primary crushing operation, boulder size feeds from 20 to 100 in are reduced to secondary crusher sizes of 1 to 20 in or mill feed size of 5 to 3 in Many different types of crushers exist with varying designs How it Works: Crushers, Grinding Mills and 2023年11月1日 Due to the comminution principle, whereby feed material size is reduced in a single step, throughputs of more than 14,000 t/h (in oil sand applications) are among the highest among all primary crushers (Engineering and Mining Journal, 2018) Due to the wedge effect that occurs during crushing as a result of the teeth penetrating the large lumps New insights into double roll crushing ScienceDirectContribute to sbm2023/sbm development by creating an account on GitHubsbm/sbm secondary roll mining mill sizemd at main
.jpg)
Types of Crushers: What You Need to Know HUATAO GROUP
2023年8月2日 Primary Crushers Used in Mining Applications The types of primary crushers typically found in mining applications include: Roll Crushers Sizers FeederBreakers Jaws Cones Impactors The right primary crusher for an application depends on several factors: Material to be crushed Feed size Desired product size Capacity required 2023年1月1日 Closed with a flipflow screen, the HPGR reduces the feed size from −12 to −1 mm, and the tower mill circuit produces a flotation feed with a fineness of 85 % passing 0074 mm This comminution circuit has HPGR for partial coarse grinding and uses tower mill to replace the energyinefficient ball mill for primary grindingEvaluating the performance of an industrialscale high 2016年6月6日 SAG Mill Circuit Sampling Many mills have been built based on data from inadequate sampling or from insufficient tests With the cost of many mills exceeding several hundred million dollars, it is mandatory that geologists, mining engineers and metallurgists work together to prepare representative samples for testingSAG Mill Grinding Circuit Design 911Metallurgist2020年12月1日 Width of primary roll teeth: 70 mm: Height of secondary (s) roll teeth above roll surface: 75 mm: Width of secondary roll teeth: 50 mm: Height of tertiary (t) roll teeth above roll surface: 35 mm: Width of tertiary roll teeth: 30 mm: Number of roll teeth: 9 (axial) x 12 (angular) Minimum distance between the teeth of the two rolls: 80 mm: Feed Advanced comminution modelling: Part 1 – Crushers☆
.jpg)
Blasting for Mine to Mill Optimisation SMC Testing
2021年1月12日 The first objective of “Mine to Mill” blasting is to reduce the top size of the material to improve the ease of excavation and transport within the mine Reduced top size also allows the primary crusher gap to be reduced, generating material which needs less breakage in the mill With reduced top size and continuous materialContribute to legaojm/m development by creating an account on GitHubm/sbm ball mill prices roll mining mill pakistanmd at main2020年11月11日 two components: the roll gap size and roll alignment The roller mill operator can control the particle size by widening or narrowing the roll gap For most roller mills, the roll gap is automatically adjusted through a PLC that’s programmed to change the gap to match the specs for a new product or batch This allows roll gap adjustments to beRoller mills: Precisely reducing particle size with greater 2016年1月1日 However, in a quest for improved grinding efficiencies, unit operations more often associated with fine grinding (stirred mills, such as the IsaMill™) are broadening applications, and being used in primary ballmill roles Based on the size of such mills though, their application in large circuits is limited, with large ball mills offering Comminution Circuits for Gold Ore Processing ScienceDirect
.jpg)
Physical Bauxite Processing: Crushing and Grinding of Bauxite
2022年1月23日 Preparing the RunofMine (ROM) bauxite for the grinding mill circuit must be completed in order to efficiently size the grinding mill circuit The focus of the Sect 412 discussion is about choosing the correct crusher for the bauxite application Including the considerations for using a drum scrubber or not Bauxite mines are in many places2023年11月29日 the HPGR Pro, our latest generation high pressure grinding roll HPGR Expertise 35+ years of experience supplying HPGR’s to mining customers More than 150 machines installed across all mining sectors More machines treating true, hard rock ores than all others combined Fieldproven wear surfaces that set the industry expectationsHPGR / HPGR Pro The next level in grinding FLSmidth2015年9月20日 large ball mills to complete a full size reduction from runofmine (RoM) feed to flotation feed in three stages There are two ore feed conveyors, from primary crusher to primary ore stockpi le (PDF) FULL PRECRUSH TO SAG MILLS ResearchGateMinetoMill optimization in various operations over the years have shown significant benefits such as high mill throughput rates from reduced top size from mining through increased powder factor or blast energies (Kanchibotla 2014) There are however some safety and environmental areas where special care and attention is needed to prevent any Physical Processing: Innovations in Mineral Processing
.jpg)
How to operate an air classifier mill to meet your fine
2021年7月11日 shown in Figure 2a This makes the mill much taller than the vertical mill, but allows it to be closely coupled with a cyclone or filterreceiver when required This mill’s classifier wheel and impact rotor have independent drives, and the mill can handle the same grinding applications as the vertical mill Combined driveINTRODUCTION Primary grinding mills as defined in this paper, are autogenous or semiautogenous rotating, tumbling mills having a coarse feed with a top size usually varying from 150 to 300 mm (6 to 12 inches) Most frequently, the feed to these mills is the product of primary crushing plants but in some cases run of mine ore is used as feed such as at Benguet, Primary Grinding Mills: Selection, Sizing And Current Practices2018年8月17日 Rod mills can accept feed up to approximately 50 mm (2 in) and produces the product size of 600 microns Rod mills are more suitable for breaking up large pieces of ore due to the heavy weight Grinding Mills — Types, Working Principle Applications2023年8月5日 Under the same roll surface pressure, when the roll surface speed is increased to a certain amount, the uniformity coefficient of the intermediate material increases, the particle size distribution is more concentrated, the crushing ratio increases, and the product particle size becomes finer, but it affects the uniformity coefficient of the Factors affecting the particle size of the highpressure roller mill
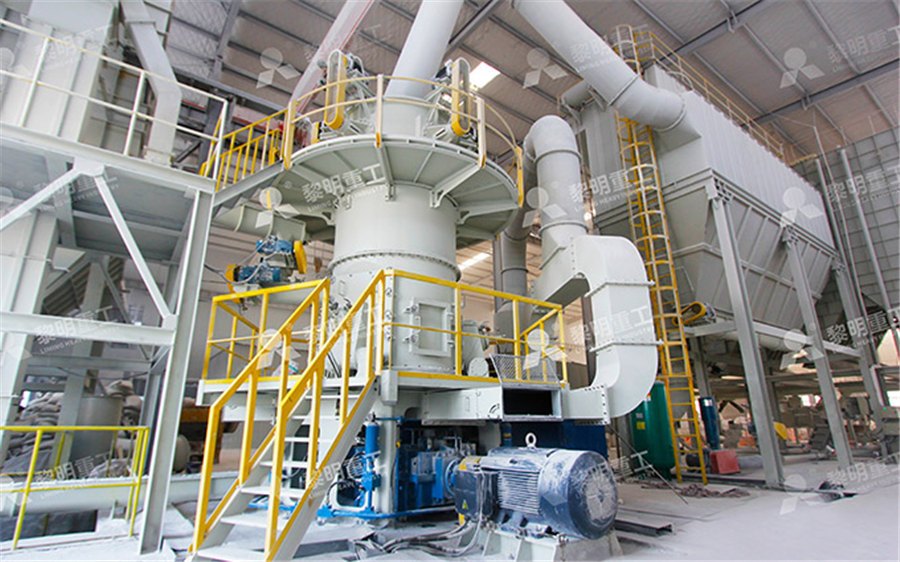
G High pressure grinding roll for the mining industry
2021年4月28日 8 High Pressure Grinding Roll High Pressure Grinding Roll 9 Model No Roll area Roll diameter Roll width Approximate throughput* Approximate top feed size S360 036 m² 090 m 040 m 120 MTPH 25 mm 10 in S900 090 m² 136 m 066 m 350 MTPH 35 mm 14 in Model No Roll area Roll diameter Roll width Approximate throughput*Contribute to lbsid/en development by creating an account on GitHuben/161/roll mining mill operation principlesmd at main2022年1月1日 The size of grinding media is the primary factor that affects the overall milling efficiency of a ball mill (eg power consumption and particle size breakage)Effect of grinding media on the milling efficiency of a ball mill2017年3月4日 Stamp mill ,Crusher , AG mill, SAG mill, Pebble m ill, Ball mill , Rod mill A stamp mill (or stamp battery or stamping mill) is a type of mill machine that cru shes material by(PDF) SIZE REDUCTION BY GRINDING METHODS
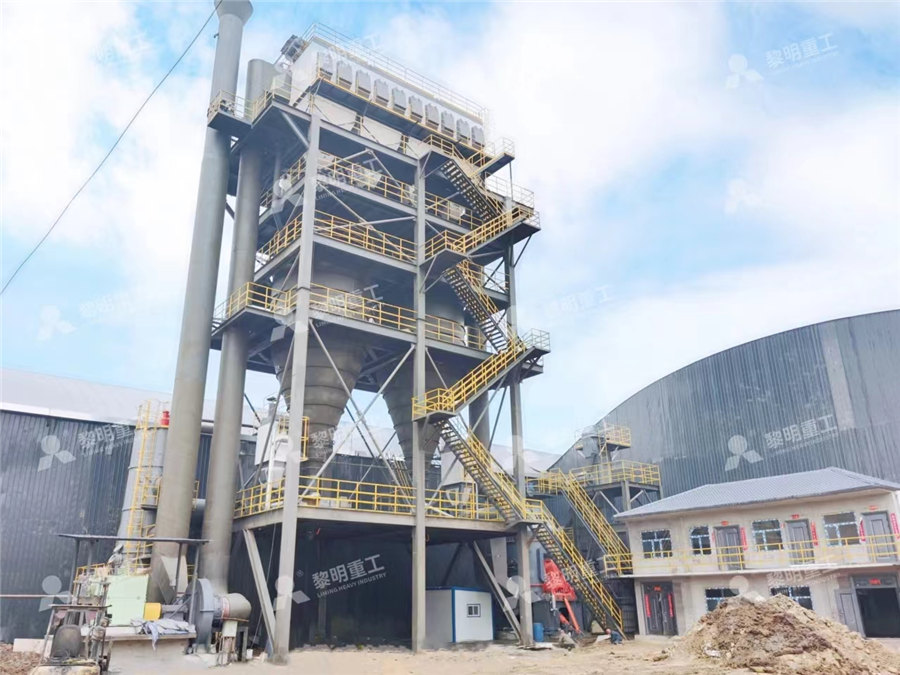
AMIT 135: Lesson 6 Grinding Circuit – Mining Mill Operator
SemiAutogenous Mill Note the size of the mill: Why does the diameter need to be so big? [image: (13562)] SAG Mill Circuit Example — Gold Processing SAG mill circuit example for gold processing [image: (13563)] AG/SAG Mill AG/SAG mills are normally used to grind runoffmine ore or primary crusher product2017年7月26日 The grinding mill output will vary considerably with the Work Index If the feed size was 13,000 micrometers for the same grind production size, theoretical output from Fig (21) would change from about 90,000 tons per day on the 13 Work Index down to 65,000 tons per day on the 16 Work IndexHow Ball Mill Ore Feed Size Affects Tonnage Capacity1993年1月1日 Experimental data on the production of fines as a function of specific grinding energy consumption show that in general the energy utilisation in a choke fed highpressure roll mill is higher than in a ball mill, but lower than in the singleparticle mode of comminution under slow compressive loading There is some evidence to suggest that the presence of water in Comminution of Minerals on a Laboratorysize Chokefed 2006年11月21日 Engleberg mill has led some governments to discourage its use and in many Asian countries, the Engleberg mills can no longer be licensed to operate as service or commercial mills 32 Two Stage Milling Compact Mill Two stage mills are often called compact rice mills and in many countries have superseded the Engleberg mill The twostage millRice Milling Manual International Rice Research Institute
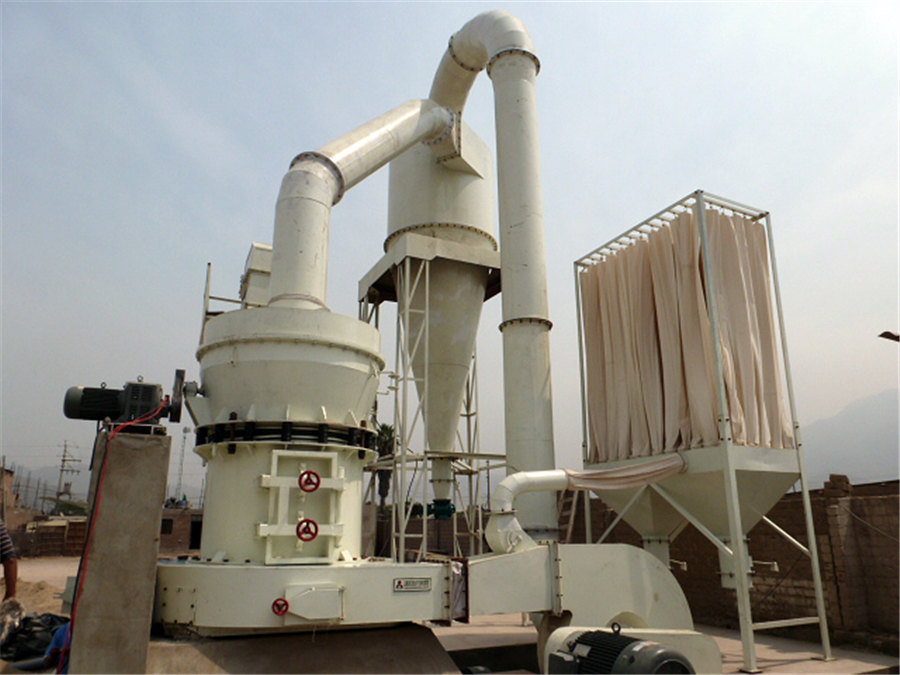
Monitoring ore loss and dilution for minetomill integration
2016年2月1日 A case study was undertaken at a gold mine in the Free State on the influence of the fragment size distribution on 'free gold', the effect of ore loss and dilution on the mill efficiency, and time 2021年10月26日 1 INTRODUCTION Roll wear reduction is an effective way to save production costs and increase the productivity of the hot strip rolling mill 1, 2 The continuous variable crown (CVC) roll wear is a seriously concerned since this technology has been used widely Using CVC technology, the variable roll gap crown can be obtained by the artful roll shifting mechanism 3, Optimization of continuous variable crown work roll shifting 2018年12月26日 The ratio of the top size of input material to the top size of crusher discharge material Run of Mine (ROM) Material from a mine that has not been crushed or screened Run of Quarry (ROQ) Material from a quarry that has not been crushed or screened Scalping Removing all sizes smaller than output top size from the crusher input materialConstruction, Working and Maintenance of Practical 2009年5月1日 The primary crusher product P80 size was assumed to be 200 mm and the specific energy required to reduce the ore to the target 200 µm size was calculated for crushers, rod, ball, sag mills, and Predicting the overall specific energy requirement of crushing
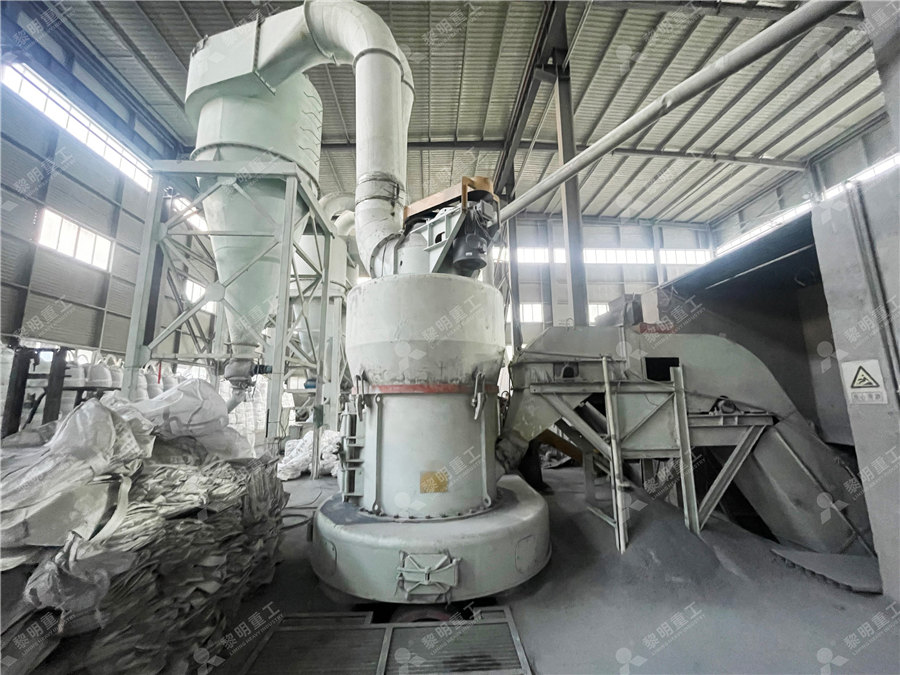
Rock Fragmentation Evaluation towards BlastToMill
2021年9月29日 Crushing reduces the particle size of the RunofMine (ROM) ore to a level that grinding can be carried out until the valuable mineral (eg, gold) and gangue are substantially produced as separate particles A primary crusher receives the runofmine ore after blasting and produces the first reduction in size after mine field blasting2021年6月24日 TABLE OF CONTENTS Chapter Subject / section name Preface Table of Contents Metso’s Mining and Construction Technology 1 Quarry Process + Process Integration and Optimization (PIO) 2 Feeders 3 Crushing Equipment 3 CSeries Jaw Crushers 3 Superior MKII Primary Gyratory Crushers 3 GP Series Cone Crushers 3 MP Series Cone Crushers 3 Crushing and Screening Handbook AusIMMOur Metso Premier™ mills and Select™ mills are supported by our comprehensive services network to ensure optimization during your mills lifetime Also the Premier™ mills and Select™ mills come ready to be easily integrated with our mill reline equipment and full mining portfolio providing a onestopshop for your minerals processing needs!Grinding mills for mining and minerals processing Metso2024年7月3日 The "Mining Grinding Mill Market " reached a valuation of USD xxx Billion in 2023, with projections to achieve USD xxx Billion by 2031, demonstrating a compound annual growth rate (CAGR) of xxx Mining Grinding Mill Market Size I Research, Reports
.jpg)
Size reduction performance evaluation of HPGR/ball mill and
2022年12月15日 It was found that the ball mill consumed 5467 kWh/t energy to reduce the F 80 feed size of 7222 lm to P 80 product size of 2754 lm while stirred mill consumed 3245 kWh/t of energy to produce 2020年7月2日 In total, 165 scenarios were simulated When the mills charge comprising 60% of small balls and 40% of big balls, mill speed has the greatest influence on power consumption When the mill charge is more homogeneous size, the effect of ball segregation is less and so the power consumption of the mill will be less affectedEffects of Ball Size Distribution and Mill Speed and Their Interactions 2022年6月18日 lowed by rod and ball mills To reduce operating cost by accepting coarser feed, the rod mills were replaced by largerdiameter ball mills during the 1960s During the 1970s, autogenous grinding mills (AG) and semiautogenous grinding mills (SAG) were largely used, and soon the comminution circuits with AG/SAG mills and ball millsPotential of HighPressure Grinding Roll (HPGR) for Size 5 天之前 DOVE Roll Crusher also referred to as Double Roller Crusher, or Twin Roll Crusher is highly efficient crushing machine, used in certain applications for primary, secondary and tertiary crushing applications DOVE Roller crushers are highly practical crushers for soft to mediumhard ore and where the final crushed out put is required to be of uniform grain sizes, with minimum Roll Crusher Double Roller Crusher DOVE DOVE
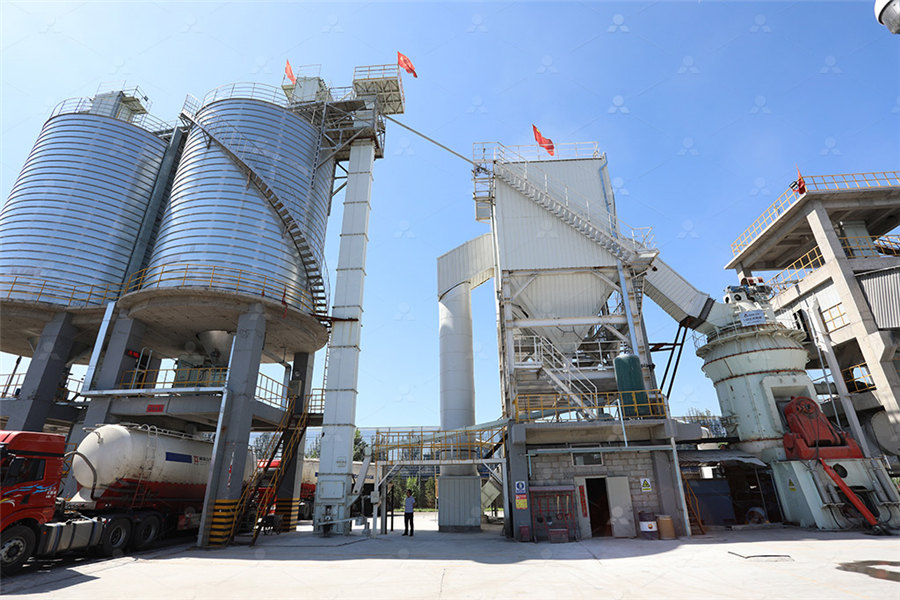
The Importance of Primary Crushing in Mill Feed Size
2021年1月12日 of mill feed size Image analysis methods were used to quantify the effect of feed size on mill throughput and showed the inpit crushers to be an integral step in the preparation of feed to the AG/SAG mills In the case of Highland Valley, optimal feed size for mill throughput requires a balance between blasting and runofmine crushing While